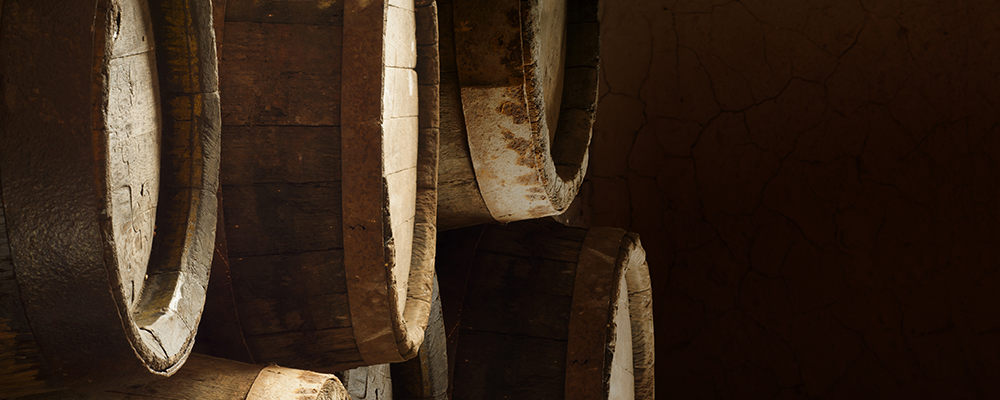
We all know that too much beer is bad for our health. Doctors are united on this. The Great Beer Flood of 1814 took this adage to a whole different level.
In a story which could be lifted from the pages of a Dickens novel, a vat containing 3,555 barrels of beer burst in Henry Meux’s Horseshoe Brewery in the parish of St. Giles, London, England. You would be forgiven for thinking that’s the opening line of a joke.
However, eight people – all women and children – died in tenements adjacent to the brewery, in a flood of more than 570 tonnes of beer.
This true story is a devastating reminder of the need for good process safety standards.
Loss of Containment is not a barrel of laughs
Various accounts of events have been bandied around but at the core of the incident is quite simply a loss of containment. According to the dusty books of history, Meux’s cavernous cask failed after 20 years of service with limited inspections to verify integrity.
On October 17, 1814, a seven-hundredweight iron hoop detached from the cask: it had secured a 22-foot tall vat.
In the aftermath of the flood, the storehouse clerk told the inquest that he was “not alarmed” as similar incidents happened two or three times a year devoid of serious consequences.
As it would be the case, on that fateful night the consequences were more than serious. A tsunami of beer crashed out of the brewery through brick walls, down streets and into homes, carrying property and people in the pull of its tide.
Damaged by the force of the bursting vat, other smaller vats collapsed, adding to the whirlpool of beer. It is believed that over 1,000,000 litres of porter flooded the neighbourhood.
What we can learn today
Contrary to popular belief, hindsight is a wonderful thing when we actually learn from it. So what can the high hazard sector learn from The Great Beer Flood of 1814? Aside from the fact that drinking at work isn’t advisable and against the law, quite a lot can be dredged from the rivers of the past.
In processing good safety standards, The Great Beer Flood tells us that site managers should:
- Carry out risk assessments to identify any potential gaps in their safety systems
- Introduce measures to close these gaps
- Understand the inner workings of their site and how to reduce or mitigate hazardous events
- Regularly inspect equipment and introduce maintenance plans
- Learn from past issues on their own sites to avoid reoccurrences
- Ensure operators are fully trained and that they report safety issues on the ground
- Draft up plans to collaborate with emergency personnel in the event of a hazard
Catastrophic events are rare but not extinct
If we turned on the TV today to find a beer tsunami had devastated large parts of London, the collective sound of jaws dropping would be heard from space. This is highly unlikely today.
Industry now faces a set of new process safety challenges. Much like the beer flood though, these are incidents which are low in frequency and high in danger.
Recent decades have, for instance, paid witness to devastating incidents such as Flixborough, Seveso, Piper Alpha, Texas City, Buncefield and Deep Water. With these still imprinted on the industrial landscape, process safety has never been more important.
So it is that we must learn from the past and plan for a safer future. We’ll drink to that.